

CONTINUOS MELT FILTER PF
The continuous melt-filtration system PF makes possible uninterrupted extrusion, even when processing highly contaminated materials. Unlike conventional screen changers, which require extensive and constant operator attention, the PF can operate automatically.
The PF is the most cost effective system available, delivering a quick return on investment.
HOW IT WORKS
As extruded material enters the unit, it passes through a stainless-steel screen plate that is micro drilled or laser perforated. The screen is hard faced, while contaminants are caught on the screen-plate surface.
When waste builds up and back pressure reaches a preset level, a rotating blade sweeps the screen, collects the contamination in the wiper chamber and then discharges it through a port. The PF handles a broad range of materials including PE, PP, PS, PC and ABS, and can operate at temperatures up to 300°C and pressures up to 200 bar.
Purging of contaminated material requires on average, less than 0,5 kg per purge a significant savings compared to conventional screen changes. The unit can also operate in a continuous-wiping mode when extremely contaminated material is being processed. In this mode, material lost in purging amounts to only 0.2% to 0.5% of overall throughput.
CONTROLS AND GENERAL INFORMATION
-
The PF comes with its own UL or CE-compliant control panel.
-
PLC and touch screen
-
Six heat zones
-
Upstream and downstream adapters included
-
Easy to install and operate
-
Single power drop

FUNCTIONALITY
-
The PF runs in automatic mode controlled by a PLC that directs all of the functions.
-
The rotating blade that wipes the screen plate clean can be actuated manually by pushing a button, or triggered automatically based on a timer or backpressure transducer.
-
The screen filter can last one to two weeks, depending on the materials processed and the percentage of contamination, typically 1000-3000 wipes.
ADVANTAGES
-
Thermal insulation for energy saving
-
Unimpeded flow through large passages
-
Tolerates up to 10% of paper/labels or cardboard
-
Can handle contaminants up 20 mm diameter
-
Minimal discharge of good material with contaminants
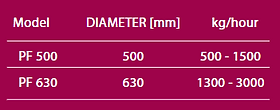
